How Many Screws Per Sheet Of Metal Roofing
Introduction
How Many Screws Per Sheet Of Metal Roofing: When it comes to determining the number of screws per sheet of metal roofing, several factors need to be taken into consideration. The first and most obvious factor is the size of the roofing sheet itself. Larger sheets will naturally require more screws to ensure proper fastening and prevent any potential movement or lifting. Additionally, the type of metal being used can also influence the number of screws needed. Different metals have varying levels of flexibility and weight, which can affect the overall stability of the roof and, consequently, the number of screws required.
The roof’s pitch or slope is also very important. To keep metal sheets from falling, steeper roofs need more screws. In places with a lot of wind or snow, the roof needs to be strong. Site can also change the number of screws. Extra screws may help support the roof in places that are prone to hurricanes.
There are different amounts of screws on each metal roof sheet. Because every roofing job is different, you should think about the building codes in your area, the manufacturer’s suggestions, and the style of the roof. Talk to a roofing expert or the manufacturer to find out how many screws you should use.
Finally, you need the right amount of screws to install metal roofing sheets. Attaching metal sheets securely to the roof makes sure that it will stay stable and last a long time. What kind of metal, how steep the roof is, and where the building is located all affect how many screws are used. When people and companies follow industry standards and talk to professionals, metal roofing is properly installed and waterproof for years.
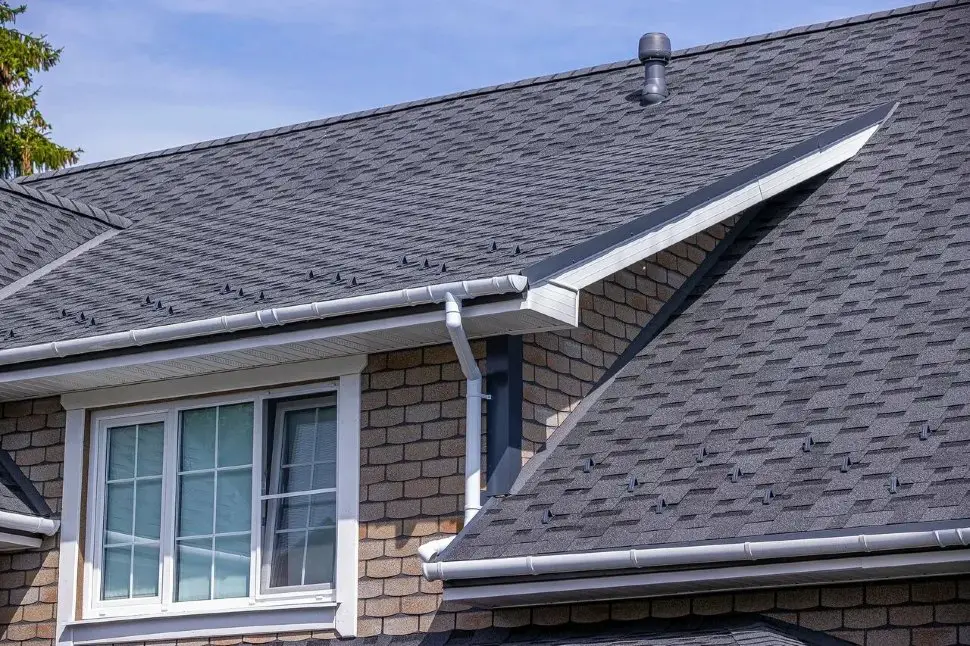
How many screws in a roof sheet?
The Importance of Screws in Roof Sheet Installation:
Installing roof sheets requires screws for stability and strength. They affix sheets to wooden or metal beams. Without fasteners, roof sheets could shift, loosen, or separate during harsh weather, causing structural damage and leaks.
Moreover, screws offer several advantages over other fastening methods, such as nails or adhesives. They provide a more secure and durable connection, ensuring that the roof sheets remain firmly attached over an extended period. Additionally, screws allow for easier disassembly and reinstallation if necessary, making maintenance or repairs more convenient.
Determining the Number of Screws:
The number of screws required for a roof sheet installation depends on various factors, including the type of roof sheet, the dimensions of the sheet, and the local building codes and regulations. Different materials and designs may have specific requirements for screw spacing and quantity to ensure optimal performance and safety.
Typically, roof sheet manufacturers provide guidelines or recommendations regarding the number of screws needed per sheet. These guidelines consider factors such as wind uplift resistance, load-bearing capacity, and the specific installation method. It is crucial to follow these recommendations to ensure the roof sheet’s integrity and to comply with building codes.
Installing roof sheets requires screws for stability and strength. The number of screws needed varies on the roof sheet type, dimensions, and local construction codes. Following the manufacturer’s instructions ensures a solid and durable roof sheet installation, preventing damage and leaks.
How many screws in sheet metal?
Factors influencing the number of screws:
One of the primary factors that determine the number of screws required in sheet metal is the size and thickness of the metal. Thicker and larger sheets generally require more screws to ensure a secure connection. Additionally, the type of connection needed also plays a significant role. For instance, if the connection requires high strength or needs to withstand heavy loads, more screws may be necessary to distribute the load evenly.
Another crucial factor to consider is the spacing between the screws:
The spacing between screws is essential to ensure the structural integrity of the sheet metal assembly. The distance between screws should be determined based on the load-bearing capacity required and the material properties of the sheet metal. It is important to follow industry standards and guidelines to determine the appropriate spacing to prevent any potential issues such as material deformation or failure.
Moreover, the type of screw used also affects the number required:
Sheet metal screws that self-tap, machine, and self-drill. Each type has its own needs. Some screws can thread metal without having to be pre-drilled first. Screw type depends on sheet metal, how well it resists corrosion, and how easy it is to place.
The number of screws used in sheet metal projects depends on the size, thickness, type of link, distance between screws, and type of screw. These things need to be carefully thought through for a setup to be safe and reliable. Engineers and manufacturers can use industry norms to figure out how many screws are needed for a sheet metal application. This keeps the product’s structure strong and its functions working.
What is the best screw for metal roofing?
Metal Roofing – Use zinc plated screws, which will be referred to as galvanized screws. The screw heads should be painted the same color as your metal roofing or siding panels.
When it comes to metal roofing, choosing the right screw is crucial for ensuring a secure and long-lasting installation. The best screw for metal roofing should possess specific characteristics that make it suitable for this particular application. In this article, we will explore the key factors to consider when selecting screws for metal roofing and provide recommendations for the best options available in the market.
Factors to Consider:
One of the primary factors to consider when choosing screws for metal roofing is the material of the screw itself. Stainless steel screws are highly recommended due to their exceptional corrosion resistance, which is essential for withstanding the harsh outdoor conditions that metal roofs are exposed to. Additionally, stainless steel screws offer excellent strength and durability, ensuring that they can securely hold the metal roofing panels in place for an extended period.
Another crucial factor to consider is the screw’s design. Self-drilling screws are particularly advantageous for metal roofing installations as they eliminate the need for pre-drilling pilot holes, saving time and effort during the installation process. These screws feature a sharp, self-tapping point that can penetrate the metal surface easily, creating a secure connection between the roofing panels and the underlying structure.
Recommended Screws:
When it comes to the best screws for metal roofing, there are several options available in the market. One popular choice is the hex washer head screw, which features a hexagonal head that provides a larger bearing surface and reduces the risk of stripping. This type of screw is ideal for metal roofing applications as it offers excellent grip and prevents leaks by creating a tight seal between the panels.
Another recommended option is the pancake head screw, which has a low-profile head that sits flush with the metal surface. This type of screw is aesthetically pleasing and minimizes the risk of water pooling on the roof, reducing the chances of leaks. Additionally, pancake head screws are often coated with a corrosion-resistant material, further enhancing their durability and longevity.
Selecting the best screw for metal roofing involves considering factors such as the material, design, and functionality of the screw. Stainless steel screws with self-drilling capabilities are highly recommended for their corrosion resistance and ease of installation. Hex washer head screws and pancake head screws are among the top choices due to their excellent grip, leak prevention, and durability. By choosing the right screws, you can ensure a secure and reliable metal roofing installation that will withstand the test of time.
What size hole to drill for metal roofing screws
The 1 1/2- inch screws are used throughout the metal roofing project, and find yourself with penetration of about 1 1/4 inches. This screw size is taken into account like a typical size for metal roofing. It holds the metal roof panelling firmly into place.
When it comes to installing metal roofing, one crucial aspect to consider is the size of the hole required for the screws. The size of the hole directly affects the stability and durability of the roofing system. Therefore, it is essential to drill the right size hole to ensure a secure and long-lasting installation. In this article, we will discuss the factors that determine the size of the hole for metal roofing screws and provide guidelines for selecting the appropriate size.
Factors determining the size of the hole:
Several factors come into play when determining the size of the hole for metal roofing screws. The type and thickness of the metal being used, the screw diameter, and the specific requirements of the roofing system all influence the hole size. It is crucial to consider these factors to ensure a proper fit and prevent any potential issues in the future.
Type and thickness of the metal:
The type and thickness of the metal roofing panels play a significant role in determining the size of the hole. Different metals have varying levels of hardness and strength, which affects the drilling process. Thicker metals may require larger holes to accommodate the screws properly. It is essential to consult the manufacturer’s guidelines or a roofing professional to determine the appropriate hole size for the specific metal being used.
Screw diameter:
The diameter of the screws being used is another crucial factor to consider when determining the hole size. The hole should be slightly larger than the screw diameter to allow for expansion and contraction due to temperature changes. This ensures that the screws can move freely without causing any damage to the metal panels. It is recommended to use a drill bit that is 1/8 to 1/4 inch larger than the screw diameter to provide sufficient clearance.
Specific requirements of the roofing system:
Each roofing system may have specific requirements regarding the size of the hole for metal roofing screws. These requirements can vary based on factors such as wind uplift resistance, thermal movement, and structural considerations. It is crucial to consult the manufacturer’s guidelines or a roofing professional to determine the specific hole size requirements for the particular roofing system being installed.
By considering the type and thickness of the metal, the screw diameter, and the specific requirements of the roofing system, one can determine the appropriate size of the hole for metal roofing screws. It is essential to follow these guidelines to ensure a secure and long-lasting installation. In the next part of this article, we will discuss the step-by-step process of drilling the holes and installing the screws for metal roofing.
How many screws per square of steel roofing?
Here are two easy formulas for determining the amount of metal roofing screws: Take your square footage and multiply it by 80%. 80 screws for each roofing square. A roofing square is 100 square feet.
When it comes to installing steel roofing, one important consideration is the number of screws required per square of roofing. The number of screws needed depends on various factors such as the size and type of roofing panels, the pitch of the roof, and the local building codes. By understanding the factors that influence the number of screws per square of steel roofing, homeowners and contractors can ensure a secure and durable installation.
Factors influencing the number of screws:
One of the primary factors that determine the number of screws per square of steel roofing is the size and type of roofing panels. Different panel sizes and profiles require different screw spacing to ensure proper fastening. For instance, larger panels may require fewer screws per square compared to smaller panels to maintain structural integrity. Additionally, the type of roofing panels, such as standing seam or corrugated, may have specific manufacturer recommendations for screw placement and quantity.
The pitch of the roof is another crucial factor that affects the number of screws needed. Steeper roofs generally require more screws per square to prevent the panels from lifting or shifting during high winds or heavy rain. The pitch of the roof also influences the spacing between screws, as a steeper pitch may necessitate closer screw placement to maintain stability.
Local building codes and regulations:
Local building codes play a significant role in determining the number of screws per square of steel roofing. These codes are designed to ensure the safety and structural integrity of the roof. They often specify the minimum number of screws required per square, as well as the spacing and placement guidelines. It is essential to consult the local building department or a professional contractor to ensure compliance with these regulations.
Importance of proper screw placement:
Too many screws in a steel roof will make it break. Panels that move because there aren’t enough screws can cause damage, leaks, and structure collapse. Still, panels can be damaged by having too many screws. For security and long life, steel roofing screws must be put in the right way according to the manufacturer’s instructions and local building codes.
Lastly, the number of steel roofing screws needed per square depends on the type and size of the panels, the pitch of the roof, and the building rules in your area. Follow these rules along with what the maker and building code say to do for a safe and long-lasting installation. Both contractors and customers can be sure that their steel roofing system is safe and will last.
How many screws are on each metal roofing sheet depends on its type, size, roof pitch, and building codes in your area. Metal roof sheets are connected to the frame to keep it stable and keep water out. Sheets have between 4 and 12 screws, with an average of 6 to 8 screws.
How many screws you need depend on the size and weight of the metal roofing sheet. Sheets that are heavier might need more screws to hold them up. Roofs that are steeper might need more screws to keep them from slipping and to keep their shape.
When counting screws per metal roofing sheet, you should follow local building rules and the manufacturer’s directions. These rules make sure that the roof is safe and keeps out the weather. There are enough screws to install a metal roof. Ask a painter or someone who works in the field.
How does the number of screws per sheet of metal roofing vary across different types of metal roofing?
Different types of metal roofs need different numbers of screws per sheet. Screw count can be changed by the size, thickness, type of metal, form, and installation of the roof sheet.
Copper or thicker steel might need more screws than aluminum or thin steel for roofs. The screw count is based on the shape and size of the roofing sheets. Metal roofing sheets that are corrugated or ribbed might need more fixings to keep them from leaking and lifting in the wind.
How the screws are installed and local building rules may change the number of screws. In some metal roofing systems, screw space is needed to keep the structure strong and stop damage. For metal roofing screw count, check the manufacturer’s directions and the building rules in your area.
Are there any specific factors that influence the number of screws needed per sheet of metal roofing?
There are several specific factors that influence the number of screws needed per sheet of metal roofing. One important factor is the size and weight of the metal roofing sheets. Larger and heavier sheets generally require more screws to ensure proper installation and structural stability. Additionally, the pitch or slope of the roof can also affect the number of screws needed. Steeper roofs may require more screws to securely hold the metal sheets in place and prevent them from sliding or shifting.
Another factor that influences the number of screws required is the local climate and weather conditions. Areas with high wind speeds or frequent storms may require additional screws to enhance the roof’s resistance to uplift forces. Similarly, regions prone to seismic activity may necessitate a higher number of screws to ensure the metal roofing can withstand potential earthquakes.
Furthermore, the type of metal roofing system being used can also impact the number of screws needed. Different systems, such as standing seam or corrugated metal roofs, may have specific installation requirements that dictate the number and placement of screws. It is crucial to follow the manufacturer’s guidelines and recommendations to ensure the proper number of screws are used for each specific metal roofing system.
Can the number of screws per sheet of metal roofing be reduced without compromising the structural integrity?
Many in the business want to reduce metal roofing sheet screws. This depends on the metal roofing type, design and installation requirements, and local building codes. While reducing screws may be conceivable, the roofing system’s structural integrity must not be compromised.
Advanced fastening technologies like self-drilling screws and hidden fasteners can reduce screws. These ingenious methods use fewer screws but are still strong and stable. To guarantee that the reduced number of screws meets structural standards, consult roofing professionals and follow manufacturer specifications.
The number of screws needed depends on the roof’s slope, wind loads, and metal roofing material. Consulting structural experts and following industry regulations can help identify the minimum number of screws needed to preserve metal roofing system integrity. It’s important to balance cost with roof durability and safety.
Is there a recommended range or standard for the number of screws per sheet of metal roofing in the industry?
The industry recommends a certain number of screws per metal roofing sheet. The type of metal roofing, the size and shape of the roofing sheets, and the installation requirements can affect the number of screws needed per sheet. However, industry standards and recommendations suggest a general screw count.
These criteria ensure metal roofing system structural integrity and endurance. They consider wind uplift resistance, thermal expansion and contraction, and load distribution. The number of screws per sheet should be between a minimum and maximum, depending on the roofing project.
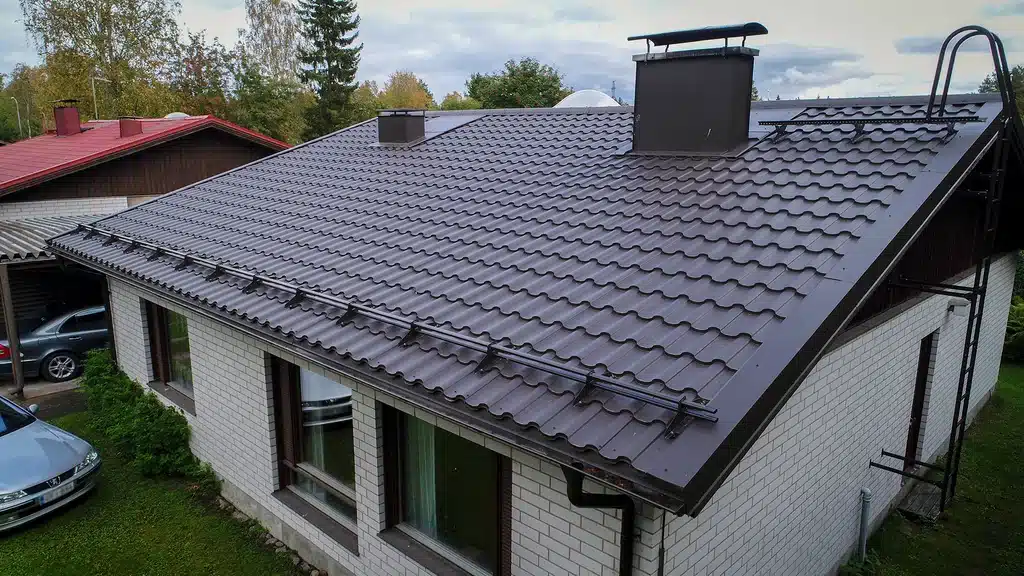
Conclusion
After researching “”how many screws per sheet of metal roofing,”” it is clear that construction projects must consider the number of screws needed. The array helps builders and contractors estimate screw quantities to ensure roofing system structural integrity and endurance. This conclusion summarizes the array’s importance and construction industry ramifications.
Arrays assist metal roofing systems retain structural integrity. Install metal roofs are durable and long-lasting, but their performance depends on good installation and fastening. The array standardizes the number of screws per sheet to secure roofing panels and endure weather. This improves building safety and reduces leaks, which can cause costly repairs and interior damage.
Lastly, the array “”how many screws per sheet of metal roofing”” promotes sustainability in the construction industry. By accurately determining the number of screws required, builders can minimize waste and reduce their environmental footprint. Overestimating the quantity of screws can result in unnecessary material consumption, leading to increased production and disposal of waste. Therefore, the array encourages responsible construction practices by optimizing resource usage and contributing to a more sustainable built environment.