How To Overlap Corrugated Metal Roofing
Introduction
How To Overlap Corrugated Metal Roofing : When it comes to overlapping corrugated metal roofing, the key is to ensure proper alignment and secure fastening. Start by measuring the length and width of the roof to determine the number of metal sheets required. It is recommended to purchase extra sheets to account for any cutting errors or future repairs. Use roofing screws or nails to secure the sheet in place, ensuring they penetrate the underlying roof deck.
As you progress with the installation, each subsequent sheet should overlap the previous one by at least one corrugation. This overlapping technique helps to create a watertight seal, preventing any moisture from seeping through the gaps. Use a level or straight edge to ensure the sheets are aligned horizontally and vertically, maintaining a uniform appearance. Secure each sheet with screws or nails, placing them in the valleys of the corrugations to avoid damaging the raised portions.
Once all the sheets are installed, it is important to inspect the roof for any gaps or loose fasteners. Tighten any loose screws or nails and seal any gaps with roofing sealant to prevent water infiltration. Additionally, consider adding ridge caps and flashing to provide extra protection against leaks at the roof’s peak and edges. By following these instructions and taking necessary precautions, you can ensure a successful and professional-looking installation of corrugated metal roofing.
With the knowledge of how to properly overlap corrugated metal roofing, you can confidently undertake your roofing project, whether it is a small shed or a large commercial building. Remember to prioritize safety and consult professional advice if needed, especially for complex or extensive installations. By investing time and effort into the proper installation of corrugated metal roofing, you can enjoy its benefits for years to come.
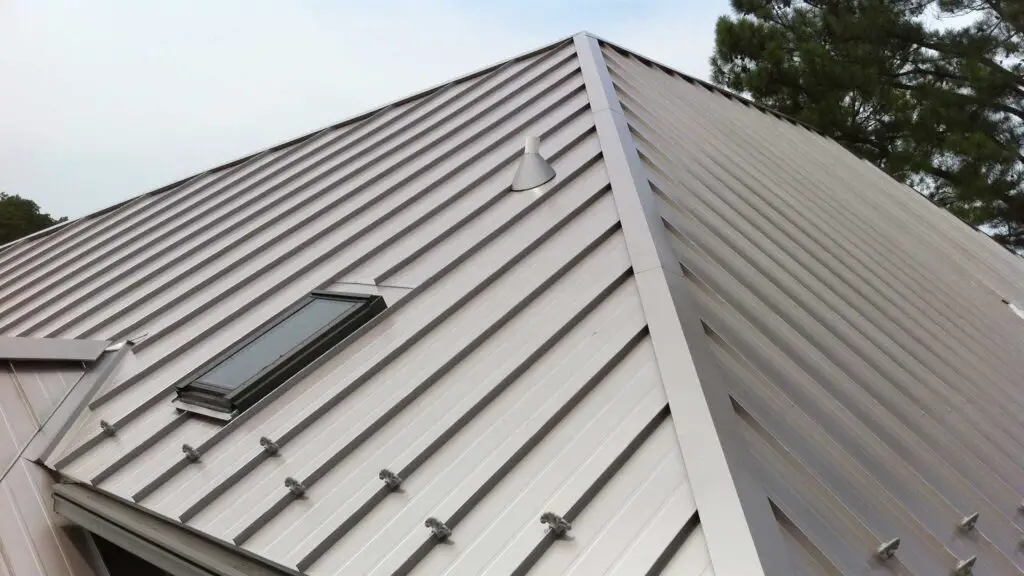
How far do you overlap corrugated metal roofing?
4 inches
When installing corrugated roofing, it’s important to consider the weather when laying it. The first step of installing corrugated metal roofing is to measure the length of the existing roof. It should be long enough so that the metal roof panels overlap at least 4 inches.
Factors influencing the overlap:
Several factors come into play when determining the ideal overlap for corrugated metal roofing. The first factor is the pitch or slope of the roof. Steeper roofs require a larger overlap to prevent water from seeping through the gaps between the panels. Additionally, the type of weather conditions prevalent in the area should also be considered.
Best practices for overlap:
It is recommended to have a minimum overlap of one corrugation, which typically translates to around 1.5 to 2 inches. This overlap provides a sufficient barrier against water penetration and helps maintain the structural integrity of the roof.
Additional considerations:
In addition to the minimum overlap, it is also important to ensure that the panels are properly aligned during installation. This means that the corrugations should line up accurately to create a continuous and seamless appearance. The appropriate overlap for corrugated metal roofing depends on various factors such as roof pitch and local weather conditions.
What is the minimum overlap for corrugated roofing?
least 60-70mm to let water to drain off without touching rafters or purlins, which can cause dampness and structural weakness.
Many homes choose corrugated roofing for its durability and affordability. It is utilized in residential, commercial, and agricultural constructions. When building corrugated roofing, the minimal overlap is crucial for performance and weatherproofing. This article discusses min overlap for corrugated roofing and its importance in ensuring a long-lasting and reliable roofing system.
Corrugated roofing requires a minimum overlap between sheets. This overlap prevents water leaks and protects the roof. The minimal overlap depends on roof pitch, corrugated roofing material, and environment.
The minimal overlap in corrugated roofing is usually one corrugation. One sheet’s end should overlap the next by at least one corrugation. This covers the spaces between the sheets to prevent water from entering. This is a broad guideline; reference the manufacturer’s instructions or local building codes for precise requirements.
In addition to the required overlap, corrugated roofing sheets must be secured using proper fasteners. Properly fitted fasteners preserve overlap and prevent sheets from shifting or lifting under adverse weather. Use screws with rubber washers or neoprene gaskets developed for corrugated roofing to provide a watertight seal.
When choosing corrugated roofing minimum overlap, roof pitch is another aspect. The roof pitch, or slope, affects overlap. Water shedding may require a bigger overlap on steeper roofs than on flatter roofs. To establish the right overlap for your roof pitch, visit the manufacturer or a specialist.
The minimum overlap for corrugated roofing is essential for watertightness and durability. Homeowners can avoid water damage and enjoy a durable corrugated roof by following the one-corrugation overlap rule and using the right fasteners. Always check the manufacturer’s instructions or local building codes for specific needs to ensure roofing system compliance and performance.
How much should you overlap corrugated tin?
An overlap of 150mm is often recommended for roofs with 10° pitches, whilst 300mm is recommended for 5° pitches. Always allow for an overhang of at least 60-70mm so that water can run off without coming into contact with rafters or purlins, which can lead to damp and structural weakness.
When it comes to installing corrugated tin, one important consideration is how much overlap is necessary. The overlap plays a crucial role in ensuring the durability and effectiveness of the tin as a protective covering. By properly overlapping the corrugated tin, you can prevent water leakage, enhance structural integrity, and prolong the lifespan of the material. In this article, we will discuss the recommended amount of overlap for corrugated tin installation.
Importance of Overlapping:
Before delving into the specific measurements, it is essential to understand why overlapping is necessary. Corrugated tin sheets are designed with ridges and valleys, allowing them to interlock when installed. This interlocking mechanism creates a barrier against water infiltration, preventing leaks and potential damage to the underlying structure. Additionally, overlapping provides added strength to the overall structure, making it more resistant to wind uplift and other external forces.
Recommended Overlap Measurements:
The recommended amount of overlap for corrugated tin installation varies depending on the specific application and environmental factors. However, a general guideline is to have a minimum overlap of one corrugation, which is typically around 1.25 to 1.5 inches. This overlap ensures sufficient coverage and allows for expansion and contraction of the tin due to temperature changes.
Factors Affecting Overlap:
While the minimum overlap guideline provides a good starting point, several factors may influence the actual overlap measurement required. The pitch of the roof, the slope of the installation surface, and the prevailing weather conditions in the area are some of the factors to consider. Steeper roofs and areas prone to heavy rainfall may require larger overlaps to ensure effective water shedding. It is advisable to consult local building codes and manufacturers’ recommendations for specific guidelines based on your location and project requirements.
Properly overlapping corrugated tin is crucial for its functionality and longevity. By following the recommended overlap measurements and considering the specific factors affecting your installation, you can ensure a durable and reliable protective covering. Remember to consult local regulations and manufacturers’ guidelines to ensure compliance and make informed decisions during the installation process.
What is the spacing for corrugated sheets?
When it comes to corrugated sheets, spacing plays a crucial role in determining their overall performance and functionality. The spacing between corrugations directly affects the strength, durability, and flexibility of these sheets. It is essential to understand the significance of proper spacing to ensure the desired outcomes in various applications. In this article, we will delve into the topic of spacing for corrugated sheets, exploring its importance and the factors that influence it.
Spacing for corrugated sheets:
Corrugated sheets are widely used in industries such as construction, packaging, and automotive due to their exceptional strength-to-weight ratio and versatility. The spacing between corrugations refers to the distance between the peaks and valleys of the waves formed on the sheet’s surface. This spacing can vary depending on the intended application and the specific requirements of the project.
One of the primary considerations when determining the spacing for corrugated sheets is the desired strength and load-bearing capacity. The closer the corrugations are, the stronger the sheet becomes. This is because the waves act as structural supports, distributing the weight evenly across the surface. However, it is crucial to strike a balance between strength and flexibility, as excessive spacing can compromise the sheet’s ability to withstand external forces and impacts.
Factors influencing spacing:
Several factors influence the spacing for corrugated sheets. The material used for manufacturing the sheets is one of the key determinants. Different materials, such as metal, plastic, or cardboard, have varying structural properties and requirements. For instance, metal corrugated sheets often have smaller spacing to enhance their load-bearing capacity, while plastic sheets may have larger spacing to maintain flexibility.
The intended application of the corrugated sheets also plays a significant role in determining the spacing. For example, in roofing applications, where the sheets need to withstand heavy loads and adverse weather conditions, closer spacing is preferred. On the other hand, in packaging applications, where flexibility and ease of folding are essential, wider spacing may be more suitable.
The spacing for corrugated sheets is a critical factor that affects their strength, durability, and flexibility. It is essential to consider the material used and the intended application when determining the appropriate spacing. Striking the right balance between strength and flexibility is crucial to ensure optimal performance in various industries. By understanding the significance of spacing, one can make informed decisions and choose the most suitable corrugated sheets for their specific needs.
What is the standard thickness of corrugated roof?
metal corrugated roofing sheet
Thickness 0.2-1.0mm. Width 760-960mm. Spread width 1000mm. Wave height 25, 28, 35, 7.
When it comes to constructing or renovating a roof, one important consideration is the thickness of the corrugated roof. The standard thickness of corrugated roof plays a crucial role in determining its durability, strength, and ability to withstand various weather conditions. In this article, we will explore the factors that influence the standard thickness of corrugated roof and its significance in ensuring a reliable and long-lasting roofing solution.
Factors influencing the standard thickness:
Several factors contribute to determining the standard thickness of corrugated roof. One of the primary factors is the intended use of the roof. Different applications, such as residential, commercial, or industrial, may require varying thicknesses to meet specific requirements. For instance, a residential roof may have different load-bearing needs compared to an industrial roof.
Another factor that influences the standard thickness is the geographical location and climate conditions. Areas prone to heavy rainfall, snowfall, or strong winds may require thicker corrugated roofs to ensure adequate protection against these elements. Additionally, the pitch or slope of the roof also affects the thickness requirement, as steeper roofs may need thicker materials to prevent water leakage.
Significance of standard thickness:
The standard thickness of corrugated roof is of utmost importance as it directly impacts the roof’s durability and ability to withstand external forces. A thicker roof provides enhanced structural integrity, making it more resistant to bending, cracking, or collapsing under heavy loads. This is particularly crucial in areas prone to extreme weather conditions, where a thinner roof may not offer sufficient protection.
Moreover, the standard thickness also affects the insulation properties of the roof. Thicker corrugated roofs provide better insulation against heat transfer, helping to maintain a comfortable indoor temperature and reduce energy consumption. This can lead to significant cost savings in terms of heating and cooling expenses over the long term.
The standard thickness of corrugated roof is influenced by various factors such as the intended use, geographical location, climate conditions, and roof pitch. It plays a vital role in ensuring the durability, strength, and insulation properties of the roof. By understanding these factors and adhering to the recommended standard thickness, individuals can make informed decisions when selecting and installing corrugated roofs.
Ultimately leading to a reliable and long-lasting roofing solution.
When it comes to overlapping corrugated metal roofing, there are several important steps to follow for a successful installation. Firstly, ensure that the roof deck is clean, dry, and free from any debris. This will provide a solid foundation for the roofing panels. Next, start by installing the first panel at the bottom edge of the roof, making sure it is aligned properly and securely fastened.
Once the first panel is in place, overlap the next panel by at least one corrugation. This overlap is crucial as it helps to prevent water from seeping through the joints. Secure the second panel in place, ensuring it is aligned with the first panel and fastened securely. Repeat this process for the remaining panels, making sure to maintain the proper overlap and alignment.
After all the panels are installed, it is important to check for any gaps or loose fasteners. These should be addressed immediately to ensure a watertight seal. Additionally, consider using sealant or roofing tape along the overlapping edges for added protection against leaks. Regular maintenance and inspections are also recommended to ensure the longevity and durability of the corrugated metal roofing.
What tools or materials are needed to properly overlap corrugated metal roofing?
When it comes to properly overlapping corrugated metal roofing, having the right tools and materials is crucial for a successful installation. Here are some essential items you will need:
Corrugated Metal Sheets: These are the main roofing material and come in various sizes and gauges. Choose the appropriate size and gauge based on your specific project requirements.
Roofing Screws: These screws are specially designed for metal roofing and have a rubber washer to prevent leaks. Make sure to use the correct length and type of screws for your metal sheets.
Screw Gun or Drill: A screw gun or drill with a screwdriver bit is essential for driving the roofing screws into the metal sheets. This will save you time and effort compared to manual screwing.
Metal Cutting Tools: You may need tin snips or a metal cutting saw to trim the metal sheets to the desired size and shape. These tools will ensure clean and precise cuts.
Roofing Underlayment: Installing a roofing underlayment beneath the metal sheets provides an extra layer of protection against moisture and helps to improve insulation. Choose a suitable underlayment material based on your climate and local building codes.
Safety Equipment: Don’t forget to prioritize safety. Wear gloves, safety glasses, and sturdy footwear to protect yourself from sharp edges and potential falls.
By using the right tools and materials, you can ensure a proper and secure overlap when installing corrugated metal roofing, resulting in a durable and long-lasting roof.
Are there any specific safety precautions to consider when overlapping corrugated metal roofing?
When overlapping corrugated metal roofing, it is crucial to prioritize safety to prevent any accidents or injuries. Here are some specific safety precautions to consider:
Personal Protective Equipment (PPE): Before starting the overlapping process, ensure that you are wearing the appropriate PPE. This includes safety goggles to protect your eyes from debris, gloves to safeguard your hands, and sturdy footwear to prevent any slips or falls.
Secure Work Area: Before climbing onto the roof, make sure the work area is clear of any obstacles or debris that could cause tripping hazards. Additionally, use caution tape or barriers to prevent unauthorized access to the work area and minimize the risk of accidents.
Proper Ladder Usage: If you need to use a ladder to access the roof, ensure that it is in good condition and placed on a stable surface. Always maintain three points of contact while climbing and descending the ladder, and never overreach or lean too far to either side.
Weather Conditions: Pay close attention to the weather forecast before starting the overlapping process. Avoid working on the roof during windy or rainy conditions, as this can increase the risk of slips and falls. If the weather becomes unfavorable while you are working, safely descend from the roof and resume the task when conditions improve.
Proper Handling of Tools: When using tools such as hammers or power drills, ensure that you are familiar with their proper usage and safety guidelines. Always maintain a firm grip on the tools and avoid using them in a careless or reckless manner that could lead to injuries.
By following these safety precautions, you can minimize the risk of accidents and ensure a safe and successful overlapping process when installing corrugated metal roofing.
How does the process of overlapping corrugated metal roofing differ from other types of roofing materials?
When it comes to overlapping corrugated metal roofing, the process differs significantly from other types of roofing materials. One key difference is the nature of the material itself. Corrugated metal roofing is made up of sheets of metal with ridges and valleys, providing strength and durability. This unique design allows for efficient water drainage and prevents leaks, making it an excellent choice for various weather conditions.
Unlike traditional roofing materials such as asphalt shingles or clay tiles, corrugated metal roofing requires a specific technique for overlapping. The sheets of metal are typically installed in an overlapping pattern, with each sheet covering a portion of the previous one. This overlapping method ensures that water flows smoothly down the roof without seeping through the gaps.
Additionally, the installation process for corrugated metal roofing may involve the use of specialized tools and materials. These can include metal screws or nails, sealants, and flashing to provide extra protection against water infiltration. It is crucial to follow the manufacturer’s guidelines and recommendations to ensure a proper and secure installation.
How does the process of overlapping corrugated metal roofing differ from other types of roofing materials?
When it comes to overlapping corrugated metal roofing, the process differs significantly from other types of roofing materials. One key difference is the nature of the material itself. Corrugated metal roofing is made up of large, flat sheets with raised ridges or corrugations. These ridges not only provide strength and durability but also create channels for water to flow off the roof. This design feature sets it apart from other roofing materials like asphalt shingles or clay tiles, which are typically installed in overlapping layers.
Another difference lies in the installation technique. With corrugated metal roofing, the sheets are typically laid horizontally from the bottom of the roof to the top, with each sheet overlapping the one below it. This overlapping pattern ensures that water is directed away from the seams and prevents leaks. In contrast, other roofing materials often require staggered or interlocking patterns to achieve a watertight seal.
Additionally, the tools and materials used for overlapping corrugated metal roofing may differ from those used for other roofing materials. While some basic tools like a tape measure, screwdriver, and drill may be common, specific fasteners and sealants designed for metal roofing may be required. It is important to consult the manufacturer’s instructions or seek professional advice to ensure the correct tools and materials are used for a successful installation.
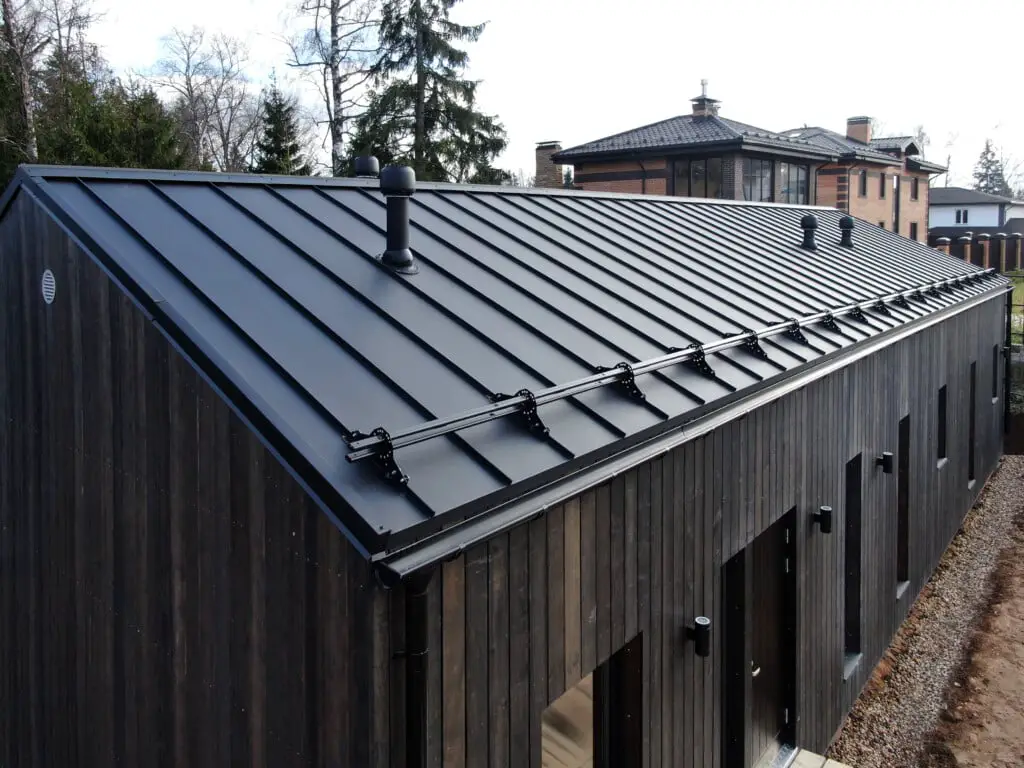
Conclusion
Overall, learning how to overlap corrugated metal roofing is a crucial skill for anyone involved in construction or home improvement projects. This technique allows for the effective installation of corrugated metal roofing, ensuring its durability and longevity. By following the instructions provided, individuals can confidently undertake this task and achieve professional-looking results.
One of the key takeaways from these instructions is the importance of proper alignment and positioning when overlapping the metal roofing sheets. This ensures that the sheets fit together seamlessly, preventing any gaps or leaks that could compromise the roof’s integrity. Additionally, the instructions emphasize the significance of using the correct tools and materials, such as roofing screws and a drill, to secure the overlapping sheets firmly in place.
Another crucial aspect highlighted in the instructions is the need for adequate safety precautions. Working with metal roofing can be hazardous, especially when handling sharp edges or using power tools. Therefore, it is essential to wear appropriate protective gear, such as gloves and safety glasses, to minimize the risk of injuries. Additionally, individuals should exercise caution when working at heights and ensure they have a stable and secure footing throughout the installation process.
In conclusion, mastering the technique of overlap corrugated metal roofing is a valuable skill that can greatly benefit individuals involved in construction or home improvement projects. By following the provided instructions, individuals can ensure a proper and secure installation, resulting in a durable and long-lasting roof. The emphasis on alignment, the use of appropriate tools and materials, and the implementation of safety precautions are all key factors in achieving professional-looking results. So, whether you are a DIY enthusiast or a professional contractor, learning how to overlap corrugated metal roofing is a worthwhile endeavor that will contribute to the success of your projects.